ASA-MIX-1
How LLC Grand Beton entered the TOP-3 of Ukrainian construction:
Unified control system ASA-MIX-1 for Concrete Mixing Plants (Simem/Stetter/Elcon etc.)

Our Client
The Grand Beton company, at the beginning of 2019, is one of the largest manufacturers of concrete, building mixtures and materials.
They turned to Automation Spirit Alliance with a request to combine all batching plants into a centralized automated control system according to European Standards.
Problems faced by the client
- Equipment from different manufacturers.
- There was no integrated automated dispatch center (ADC).
- High error in the preparation of mixtures (frequent errors in dosing materials).
- Insufficient information and non-consolidated reporting.
- Incorrect and incomplete information about the course of production processes.
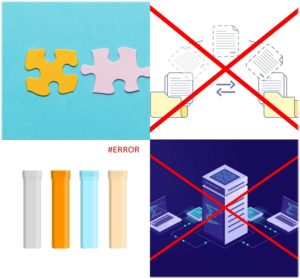
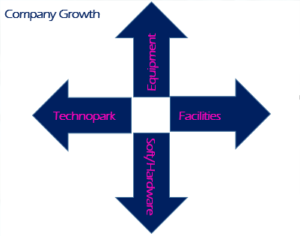
Tasks set by the client
In the phase of active growth of the company Grand Beton over the course of several years, production facilities were added, a technopark was formed, and equipment was purchased. As a result, plants were equipped with various Soft and Hardware (up to controllers) from Meka, Simem, Stetter, etc.
The chosen strategy for the development of the enterprise required prompt changes to the configuration of work units, refinement and optimization of software.
Tasks set by the client
What the client wanted:
- Consolidation of all operating plants of the enterprise into a single system.
- Arrangement of an automated dispatch center (ADC).
- Integration with an ERP system for collecting and exchanging credentials.
- Increasing productivity, dosing speed, reducing errors that occur, optimizing logistics.
- Increase operational monitoring at various stages of production and detailed reporting.
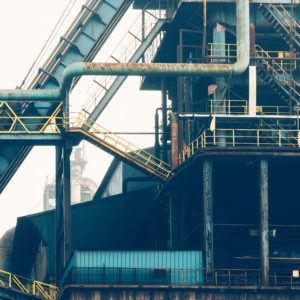
Solutions provided by Automation Spirit Alliance
Installed a comprehensive solution for the automation of all existing plants (ASA-MIX-1) and updated all workstations.
We connected all PLC from different manufacturers of existing plants by installing a unified ADC for all CMP.
Consolidated and integrated into ERP the entire reporting system with detailed analytics.
Optimized the speed and accuracy of dosing due to the “smart” algorithms ASA-MIX-1.
We provide support to the client after the implementation and launch of our software.
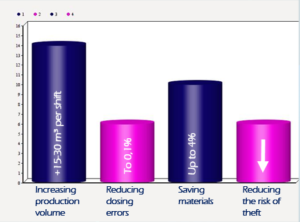
Results achieved
- Increasing the speed and accuracy of dosing, which led to an increase of 15-30 m³ per shift.
- Integration of all reporting into the customer’s ERP system.
- Reducing the risk of theft at different stages of production.
- Reducing dosing errors to 0.1%.
- Reducing material consumption up to 4%.
- Improvement of the existing logistics system.
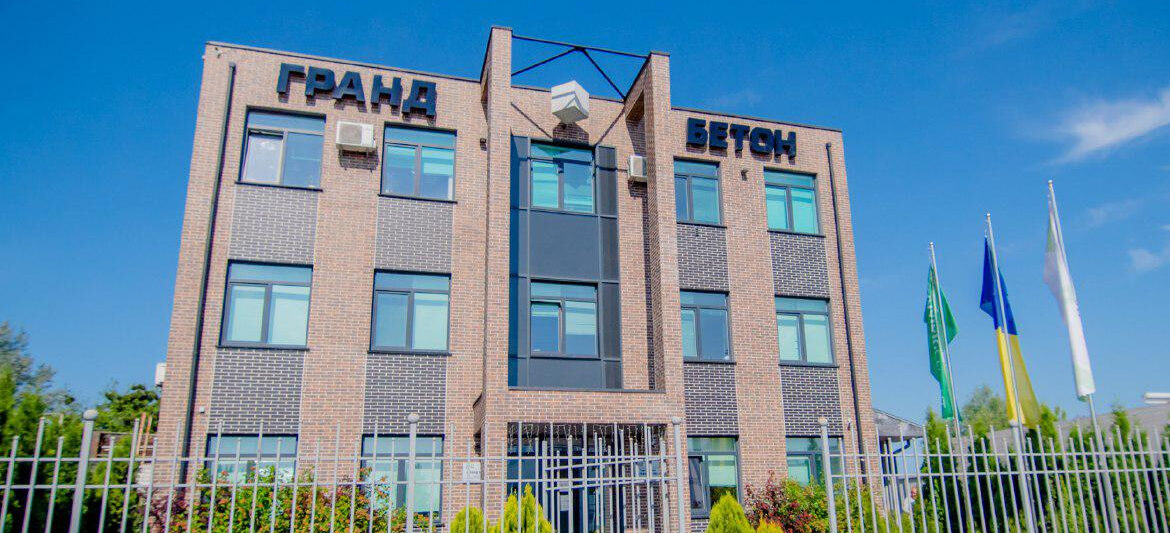
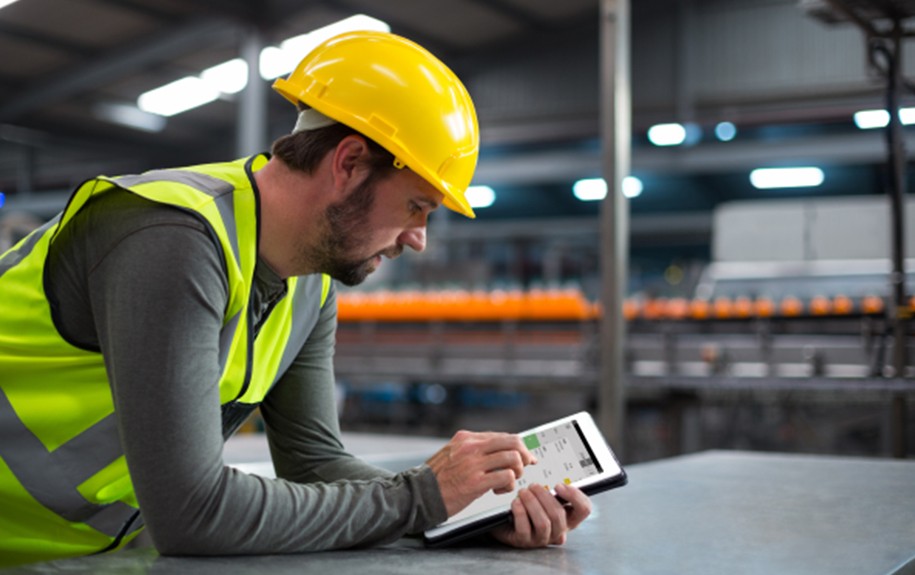