JSC TNK "KAZCHROME
The set task.
Development and implementation of the software and hardware complex of the automatic process control system for gas purification of ferroalloy electric furnaces at Aksu ferroalloy plant.
The proposed solution is as follows
The composition of the automated process control system largely determined the requirements of the terms of reference for dust protection and increased vibration resistance of the used hardware. These requirements were related to the fact that the operator’s workstation and the rack with controllers were planned to be installed in the operator’s room, where the conductive dust could penetrate and where the floor would inevitably vibrate due to the presence of powerful smoke exhausters in the same enclosure. All this had to be taken into account in the design.
The composition of the upper level of the PTC included:
Workstation (PC) of the upper level – 2 pcs.
Printer, connected to one of the PC system units and available for use with any PC – 1 pc.
APC SmartUPS 700 uninterruptible power supply – 2 pcs.
The lower level of PTC includes:
Rack of PROLINE series (made by Schroff) with redundant controller and non-redundant TBI24LC boards by Fastwel with input-output modules OpenLine series 70L and 73L by Grayhill. Total number of boards TBI24LC – 21 pieces.
Receiving and issuing of signals in the rack is done through WAGO terminals.
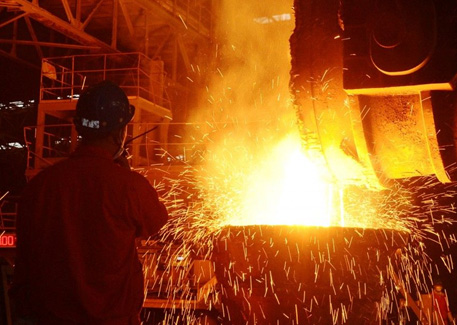
Executed works and achieved results
Software of the automatic process control system was created with the help of CAD tools and allowed to implement all the previously formulated objectives of the automated process control system. It consists of subsystems of upper (SCADA) and lower (SOFTLOGIÑ) levels. The APCS has been successfully implemented and put into operation. Successful experience in operation of PTC ACS TPMS of gas treatment of electric furnaces of Aksu ferroalloy plant confirmed the correctness of the stated technical solutions.

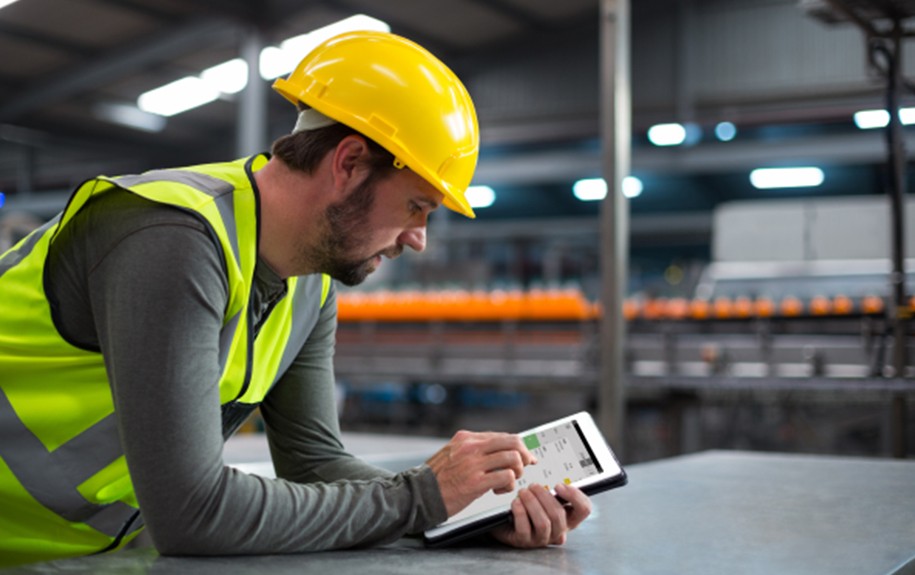